118 years of product and process innovation at Accumalux
From producing mining explosives in 1906 to leading in injection molding for battery components today, continuous innovation has driven ACCUMALUX's century-long success. Luxinnovation is providing strategic support to foster the company's growth in the coming decades.
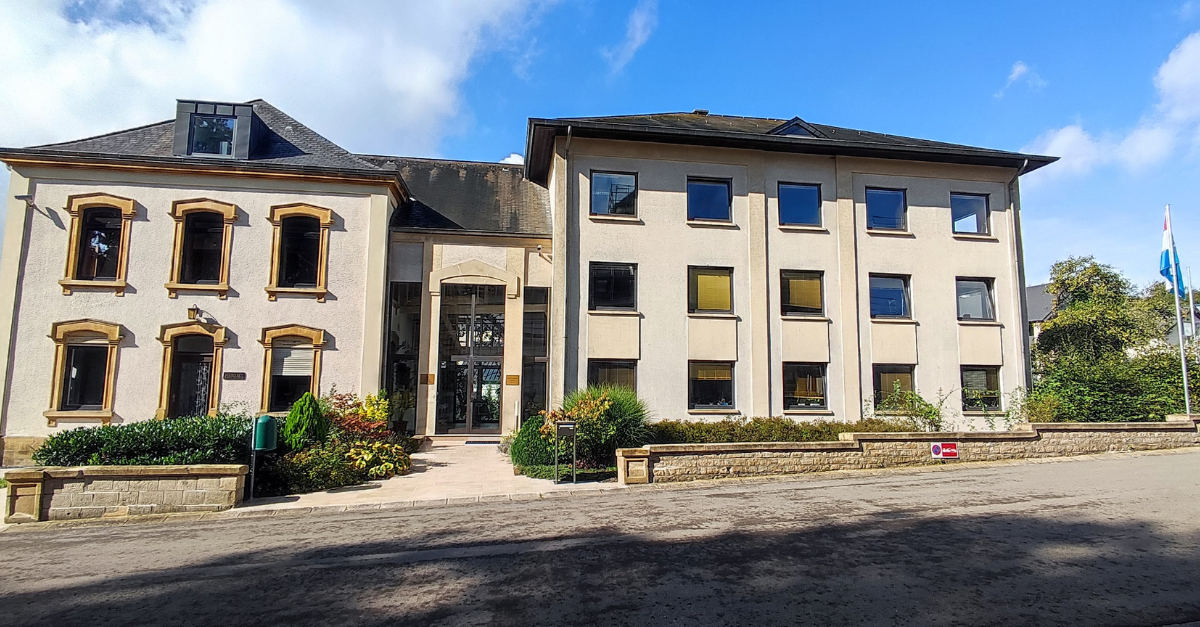
Maintaining relevance for over a century is a rare achievement for any company. Research conducted by innovation consulting firm Innosight on S&P 500 firms reveals that very few corporations survive for more than 100 years. In fact, the average lifespan of companies has been decreasing since the 1960s, from around 33 years to approximately 21 years in 2020. This figure is expected to shrink further, ranging from 15 to 20 years by 2030. So how has the Luxembourg-based business ACCUMALUX sustained 118 years of relevance and continued growth? The answer lies in a relentless focus on innovation.
“To give you a little bit of history, everything started in 1906 when the company was producing explosives for mining operations, particularly for steel production. In 1976 we pivoted to plastic injection molding solutions for the battery industry,” explains Gaël Meneghin, Director of Engineering at ACCUMALUX Group.
We automated the entire process from product assembly to storage, significantly increasing our overall efficiency and ensuring our production processes remain at the forefront of industry standards.
Gaël Meneghin, ACCUMALUX Group
The company specialises in producing essential components that support battery systems, such as boxes, lids, and accessories. These products cater to various types of batteries, including SLI (Starting, Lighting, and Ignition) batteries, motive power batteries for equipment like forklifts, and reserve power batteries used in critical infrastructure such as data centers, nuclear plants, and hospitals. “People often think that we produce batteries, but our focus is on everything around the battery itself, particularly lead-acid batteries, although we are increasingly working with lithium-ion and other battery technologies.”
Today, the group operates five production plants across four countries, with over 80 injection molding machines, welding stations, and finishing lines, achieving an annual production capacity of 30 million battery sets. Its products are shipped to about 30 countries worldwide.
Cutting-edge product innovations transforming markets
Process and product innovation, adaptability to new technologies, and strong leadership have all contributed to the outstanding growth of this IATF 16949 certified company, which holds the highest quality management standard in the automotive industry.
“Instead of importing, we’ve been producing our own injection molds since 1996. This is one of our core strengths,” notes Mr. Meneghin. ACCUMALUX’s in-house mold technology ensures precision and quality across its product range, giving the company a competitive edge in the market.
Our goal is to continue innovating and finding new applications for our injection molding expertise.
Among its significant product innovations is the patented double lid for batteries, trusted by industry leaders like Volkswagen. “Introduced about 20 years ago, it’s a game-changer for battery safety,” says Mr. Meneghin. “It delays the release of acid in the event of an accident and reduces the risk of explosion by preventing motor flames from reaching the battery’s interior. It’s still one of our most highly regarded products on the market.”
During the Covid-19 pandemic, ACCUMALUX implemented Automated Guided Vehicles (AGVs) in its production facilities, a move supported by Neistart subsidies. “AGVs have been a major step forward in our digitalisation efforts,” Mr. Meneghin explains. “We automated the entire process from product assembly to storage, significantly increasing our overall efficiency and ensuring our production processes remain at the forefront of industry standards.”
Market diversification and new applications
The company is now venturing into new markets, such as intralogistics, where it provides solutions using in-mold labeling (IML) methods. “Our goal is to continue innovating and finding new applications for our injection molding expertise. The team I manage is very forward-thinking. We support the ideas of our customers, but we also propose our own innovations, collaborating closely with them until the product is validated,” points out Mr. Meneghin.
Our goal has always been to create products that are not only durable but also offer long-lasting value.
For example, ACCUMALUX has collaborated with notable companies such as high-pressure gas valves manufacturer Rotarex and has also produced durable plastic containers for the food wholesaler La Provençale. Each container features integrated barcodes, enhancing their reusability. “We incorporated barcodes labels into the trays to promote multiple uses. Our goal has always been to create products that are not only durable but also offer long-lasting value, further reinforcing our commitment to sustainability.”
A shining example
ACCUMALUX’s digital transformation and highly automated production processes will be highlighted during the upcoming 2024 L-DIH ON TOUR, where the company will showcase its digital maturity. “We want to share our story and experiences with other companies,” states Mr. Meneghin. “We hope to inspire others to innovate and evolve as we have.”
The company is currently completing the initial and advanced digital maturity assessments offered by the Luxembourg Digital Innovation Hub. It is also exploring various other support instruments provided by Luxinnovation to bolster its future innovation efforts.
“Supporting all companies to innovate is not just our mission; we take great pride in helping to transform ideas into reality,” underscores Joachim Clemens-Stolbrink, Senior Advisor Digital Transformation at Luxinnovation.