World-class stages powered by technology
Waagner Biro Luxembourg Stage Systems has been pushing the limits of stage technology and automation with its unique computer-aided theatre solution. Its collaboration with software factory Kreios enabled a significant leap forward.
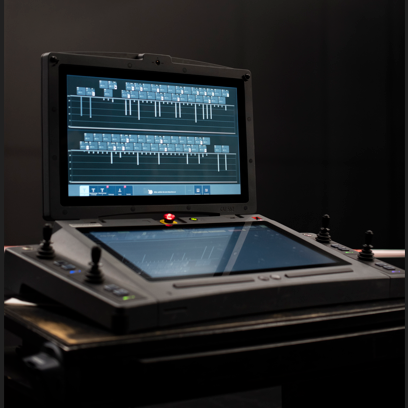
About 30 years ago, stage operations involved minimal automation—no computers, few motors, and most transitions were done manually with ropes, especially when the curtain was down. However, as stage sets grew heavier and the need for rapid, precise movements increased, motorised equipment was introduced. This led to the adoption of computers to control more complex scenic movements, which required careful coordination.
Waagner Biro Luxembourg Stage Systems, part of the Austrian group of companies, specialises in developing secure control systems for stage machinery. From the Sydney Opera House to the Vienna State Opera, the Grand Théâtre or the Philharmonie in Luxembourg, its computer-aided theatre systems (abbreviated as C⋅A⋅T) has been transforming the standards for opera houses, theatres, and concert halls worldwide.
“In 1989, we got our first theatre contract,” recalls Jean-Marie Schiltz, CEO of Waagner-Biro Luxembourg Stage Systems, formally known as Guddland Digital. “We there in the very first moment when computers were introduced on stage and we took this opportunity.”
We wanted to develop a new system as easy to use as an iPhone, and we were looking for a partner who could bring us new techniques.
Jean-Marie Schiltz, Waagner-Biro Luxembourg Stage Systems
A significant step was taken when the collaboration with Sandweiler-based software development company Kreios was formed. Kreios has been in business for more than two decades and specialises in developing technological solutions that enable clients to harness emerging innovations and gain a competitive edge.
By combining modern software engineering competences and advanced mechanical engineering expertise, the partnership between Kreios and Waagner Biro, led to the development of a fifth-generation C⋅A⋅T control system. This partnership was driven by a shared vision to create a solution that is as intuitive and accessible as a smartphone while maintaining strict safety standards.
Taking the first bold step
Developing the C⋅A⋅T V5 system began with a need for modernisation. At the time when it was developed, nothing similar existed on the market. "In 2010, our clients were requesting for a software with a more modern look and feel," explains Mr Schiltz. “We wanted to develop a new system as easy to use as an iPhone, and we were looking for a partner who could bring us new techniques,” he adds.
Following the introduction of both companies by a mutual contact, a long-term partnership began. “At first, the scope was based on test driven development, and then later it went more in depth on the project, and helping with the architecture,” points out Christian Hillerkus, Managing Partner at Kreios. “Over time, we found that we worked well together. And we then got more and more responsibility. Eventually, colleagues from Waagner Biro and myself created the new system architecture for what is now called the C⋅A⋅T V5.”
Design and UX
The C⋅A⋅T V5 system, was developed in 2016 and went live in 2018. It introduced several innovative features that set it apart from existing solutions. "All of the other systems at the time had this resistive touch interface that could detect a finger if you pressed hard enough. We were one of the first to have like a 10-finger multi-touch control desk and a 3D simulator stage built-in," states Mr Hillerkus. These innovations were crucial in enhancing the user experience (UX), allowing operators to program and run movements with unprecedented precision and flexibility. The control desks can also be custom-built to specification, which add a unique layer to it.
We were one of the first to have like a 10-finger multi-touch control desk and a 3D simulator stage built-in.
Christian Hillerkus, Kreios
In its contacts with the national innovation agency, Luxinnovation, the company was also made aware of the importance of incorporating design into its innovation efforts. As a result, its solution now stands out from others in terms of design.
“I’m pretty sure that this is the very first stage control system ever designed by a designer. If you had seen the applications back then, and even partly today, they're built by engineers. But people operating this type of machinery are not engineers. I think Waagner Biro was able to bring UX and design together,” notes Mr Hillerkus.
Safety first
Beyond these advanced features, the collaboration also took into consideration stringent safety standards. "Waagner Biro has always been a leader in safety, this is very much inherent in our thinking," emphasises Mr Schiltz. “We have a two-channel system where two computers must both open the brakes to enable the motors to move,” he states, as an example. This dual-channel approach ensures that any potential failures are mitigated. The high stakes involved makes projects in the theatre space peculiar.
According to Mr Hillerkus, unlike in the finance industry, for instance, where bugs can be fixed over time, a failure during a live stage performance could potentially lead to physical injury or even loss of life. This necessitates a different approach to system design and maintenance, with a strong emphasis on reliability and real-time problem-solving.
Non-stop innovation
Both companies are still committed to ongoing innovation and development, exploring new technologies and strategies to further enhance stage automation. “The project is stable now, and Waagner Biro is continuously investing into it. We also have people working on it on our side together with them,” notes Mr Hillerkus.
In retrospect, he concludes: "C⋅A⋅T V5 is probably one of the most challenging projects that I've ever engaged in, in all of my professional careers, but it was also one of the most interesting because we did so many things pushing the boundaries on so many levels.”
Photo credit: Ann Sophie Lindström